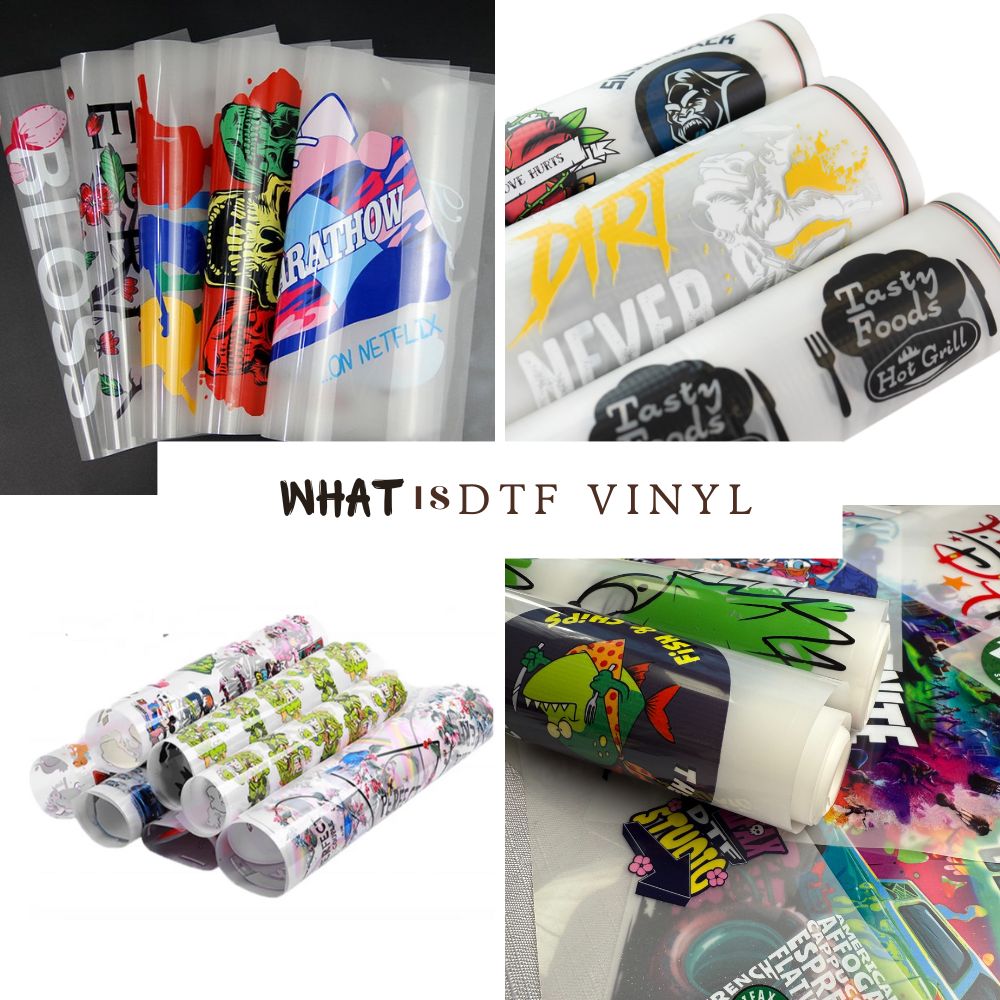
What is DTF Vinyl: Complete Guide to Direct-to-Film Printing
Introduction
What is DTF vinyl and why is it revolutionising the custom printing industry? DTF (Direct-to-Film) vinyl represents an innovative printing technology that works by applying special inks onto clear film, adding adhesive powder, and using heat to transfer designs onto fabric.
The popularity of what is DTF vinyl technology stems from its versatility across fabrics, ability to create vibrant designs, and accessibility for businesses of all sizes. Whether you're a business owner looking to expand product offerings, a hobbyist creating personalised items, or a print shop adding new services, understanding what is DTF vinyl can transform your custom printing capabilities.
What is DTF Vinyl?
What is DTF vinyl at its core? DTF vinyl is a heat transfer printing method that creates designs on PET (polyethylene terephthalate) film before transferring them to various materials. Unlike traditional heat transfer vinyl (HTV) that requires cutting and weeding, what is DTF vinyl printing produces complete designs with no weeding needed.
The basic components include:
- PET film: A clear, heat-resistant sheet that temporarily holds the design
- White and CMYK inks: Creates vibrant designs on any color fabric
- Adhesive powder: Bonds the inks to fabrics when heated
- Heat press: Transfers the design from film to fabric
Developed around 2016-2017, what is DTF vinyl technology filled a market gap by combining the detail of DTG printing with vinyl transfer versatility.
How DTF Vinyl Works: The Process Explained
The what is DTF vinyl printing process involves six key steps:
-
Design Preparation: Your design is processed through RIP (Raster Image Processor) software, which prepares it specifically for DTF printing by creating color separations and the white underbase layer.
-
Printing onto PET Film: The printer first applies a white ink underbase on the PET film, followed by CMYK inks to create the full-color image in mirror form.
-
Applying Adhesive Powder: While the ink remains wet, hot-melt adhesive powder is evenly distributed across the printed design, sticking only to inked areas.
-
Curing the Adhesive: The film passes through a curing device (320-350°F/160-177°C) to melt the adhesive powder into a smooth layer.
-
Transfer Preparation: Once cured, the transfer can be used immediately or stored for future application.
-
Heat Pressing: A heat press applies pressure and heat (approximately 330°F/165°C for 15-20 seconds) to transfer the design to the fabric.
Equipment needed for DTF printing includes:
- DTF printer with white ink capability
- DTF inks and PET film
- Adhesive powder and application system
- Curing device and heat press
- Computer with design/RIP software
Advantages of DTF Vinyl
Understanding what is DTF vinyl requires recognising its key advantages:
-
Versatility Across Fabrics: Works on cotton, polyester, blends, nylon, leather, and even waterproof materials.
-
Vibrant Full-Color Results: Creates bright designs with a wide color range. The white underbase helps colours pop on dark fabrics.
-
No Weeding Required: Unlike traditional vinyl, DTF printing puts ink only where needed, saving time on complex designs.
-
Excellent Durability and Stretch: Withstands multiple wash cycles without cracking and stretches with the fabric, ideal for athletic wear.
-
Soft Hand Feel: DTF prints feel soft to the touch—not thick or plastic-like—enhancing wearer comfort.
-
Detailed Designs and Photorealistic Images: Reproduces fine details and smooth colour transitions that other methods can't achieve.
-
Cost-Effective for Small Runs: Economical for 1-50 items with no setup time or screens required.
Disadvantages and Limitations
While what is DTF vinyl offers many benefits, consider these limitations:
-
Initial Investment: Entry-level setups cost $1,500-$3,000, with professional systems reaching $10,000+.
-
Learning Curve: Multiple technical steps require practice to master, often resulting in material waste during the learning phase.
-
Adhesive Powder Challenges: Achieving even powder application requires practice—too little causes poor adhesion; too much creates stiff prints.
-
Storage Requirements: Transfers must be kept in cool, dry environments away from sunlight, preferably in sealed containers.
-
Durability Comparisons: Generally less durable than screen printing (30-40 washes vs. 50+) and sublimation, with potential yellowing in white areas over time.
DTF vs. Other Printing Methods
DTF vs. Screen Printing
- Setup: DTF requires no screens; screen printing needs separate screens for each colour
- Quantity: DTF excels at small runs (1-50); screen printing is better for large orders (100+)
- Detail: DTF handles fine details easily; screen printing excels with solid colours
- Durability: Screen printing typically lasts longer
- Versatility: DTF works on more fabric types
DTF vs. DTG (Direct-to-Garment)
Learn more about the differences in our detailed DTG vs DTF comparison.
- Materials: DTF works on virtually any fabric; DTG works best on cotton
- Pretreatment: DTF needs no garment pretreatment; DTG often requires it
- Equipment Cost: DTF equipment is generally less expensive
- Production: DTF creates storable transfers; DTG prints directly onto garments
DTF vs. Traditional HTV
- Colours: DTF produces full-colour prints in one transfer; HTV requires layering
- Preparation: DTF needs no cutting or weeding; HTV requires both
- Detail: DTF handles complex designs better than HTV
- Feel: DTF has a softer feel; HTV can be thicker and more plastic-like
DTF vs. Sublimation
- Fabric Requirements: DTF works on any color/material; sublimation needs white/light polyester
- Durability: Sublimation is permanent; DTF eventually shows wear
- Colour Options: DTF can print white on dark fabrics; sublimation cannot print white
Applications and Use Cases
What is DTF vinyl good for? It excels in these applications:
-
T-shirts and Apparel: Perfect for custom clothing with detailed designs on various fabrics
-
Hats and Caps: Works well on curved surfaces and different headwear materials
-
Bags and Accessories: Adheres to canvas, nylon, and even some treated leathers
-
Small Business Production: Enables professional-quality products without massive investment
-
One-Off Custom Designs: Economical for unique items without minimum order requirements
-
Small to Medium Production Runs: Ideal for 1-50 identical items with efficient workflow
Getting Started with DTF Vinyl
Category |
Details |
Required Equipment |
• DTF printer with white ink capability • PET films for DTF printing• DTF inks (CMYK + White)• Hot melt adhesive powder• Powder application system• Curing device• Heat press• Computer with design/RIP software |
Budget Considerations |
• Entry-level: $1,500-$3,000• Professional: $4,000-$10,000+• Per-print: $0.50-$2.00• ROI after 300-500 prints |
Tips for Beginners |
• Start with simple designs• Practice on scrap fabrics• Control environment (65-75°F, 40-60% humidity)• Join online communities |
Common Mistakes |
• Skipping printer maintenance• Incorrect powder application• Wrong temperature/pressure• Improper transfer storage |
For detailed instructions on application, check out our guide on How to Apply DTF Transfer.
DTF Vinyl Maintenance and Best Practices
Proper maintenance ensures optimal results with what is DTF vinyl technology:
Storage: Keep transfers in cool, dry places away from sunlight in sealed containers with silica gel. Use within 3-6 months for best results.
Washing: Turn printed items inside-out, wash in cold water on gentle cycle. Avoid harsh detergents, bleach, and fabric softeners. Air-drying is preferable.
Printer Maintenance: Perform daily nozzle checks, run cleaning cycles when needed, and print regularly to prevent dried heads. Shake white ink cartridges before use.
Troubleshooting: For adhesion issues, check heat press settings; for color problems, clean print heads; for powder application issues, ensure ink is wet when applying powder.
Environmental Considerations
What is DTF vinyl's environmental impact? Several aspects merit consideration:
-
Many DTF inks are water-based with fewer harmful chemicals than solvent alternatives
-
Precise ink application minimizes waste compared to screen printing
-
No weeding waste unlike traditional vinyl cutting
-
PET films can be recyclable, with some manufacturers offering biodegradable options
-
On-demand production reduces excess inventory and resource consumption
For environmentally conscious businesses, newer technologies like UV DTF offer additional eco-friendly benefits.
The Future of DTF Vinyl Technology
The DTF printing industry continues to evolve with emerging trends:
-
Automation: Systems that handle multiple steps without human intervention
-
Multi-function Printers: Equipment that switches between DTF, DTG, and UV printing
-
Improved Formulations: Better inks for washability, stretchability, and color vibrancy
-
Advanced Print Heads: Technology allowing finer details and faster print speeds
-
Market Growth: Industry projections suggest 12-15% annual growth through 2030
DTF is democratizing access to high-quality printing technology, enabling small businesses to compete with larger operations and reshaping business models toward on-demand production.
Conclusion
What is DTF vinyl technology? In summary, it represents a significant breakthrough in custom printing, offering a balance of quality, versatility, and accessibility previously unavailable. Its ability to produce detailed designs on various fabrics while maintaining a soft feel makes it attractive for businesses of all sizes.
For those considering DTF technology, start with a complete entry-level system rather than piecing together components. Begin with simple designs on standard cotton t-shirts before expanding to complex projects. Calculate ongoing costs of consumables and maintenance when planning your business model.
Next steps for those interested in DTF technology include researching current equipment options, joining online communities, requesting sample prints, and creating a business plan that identifies your target market. With the right approach, DTF vinyl technology offers an exciting opportunity to create professional-quality custom products with relatively low barriers to entry.